GREAT DESIGN LEADS TO FACILITY FLEXIBILITY
Chelsea Piers, a space outfitted with top-of-the-line safety and utility products designed specifically for the site. To begin we created a separate, detailed quote for each area of the facility; on a project of this scale, we recommend this approach to allow for flexibility for changes and alterations so that each phase of the project can move at its own pace without delays. Next, our engineers gathered architectural plans and photographs that laid the groundwork for the design phase that would follow.
The first stage of the design phase was to create shop drawings of each unique athletic space. At Chelsea Piers, our Engineers took special considerations for the Backdrop Curtains in the large turf area (Pictured above). The turf is encircled by a running track, so our Engineers designed curtains that can stop a flying lacrosse ball almost instantly. The custom curtains also include reinforced blocks of solid vinyl behind each goal, increasing durability and performance. Another custom feature is the array of Motorized Gym Divider Curtains that divide the large turf space into multiple zones of play. These massive curtains are designed to hug the slope of the ceiling above and lie flush with the turf surface below. With the turn of a key switch, both curtains in each set retract toward the ceiling using a single winch. For the wood-floored gymnasium area, our Engineers designed custom curtains with tracks that comply with NCAA requirements for overhead clearance in competitive volleyball.
The Backdrop Curtains in the tennis court area of Chelsea Piers were designed with foot traffic in mind. These custom curtains feature a blend of track and cable supports that grant the space greater egress, flexibility, and durability. At Putterman Athletics we consider customer service a top priority. That is why we emphasize Project Management as a critical element in the success of any job. Chelsea Piers was no exception. Take a look at our process below.
Engineering Project
Management
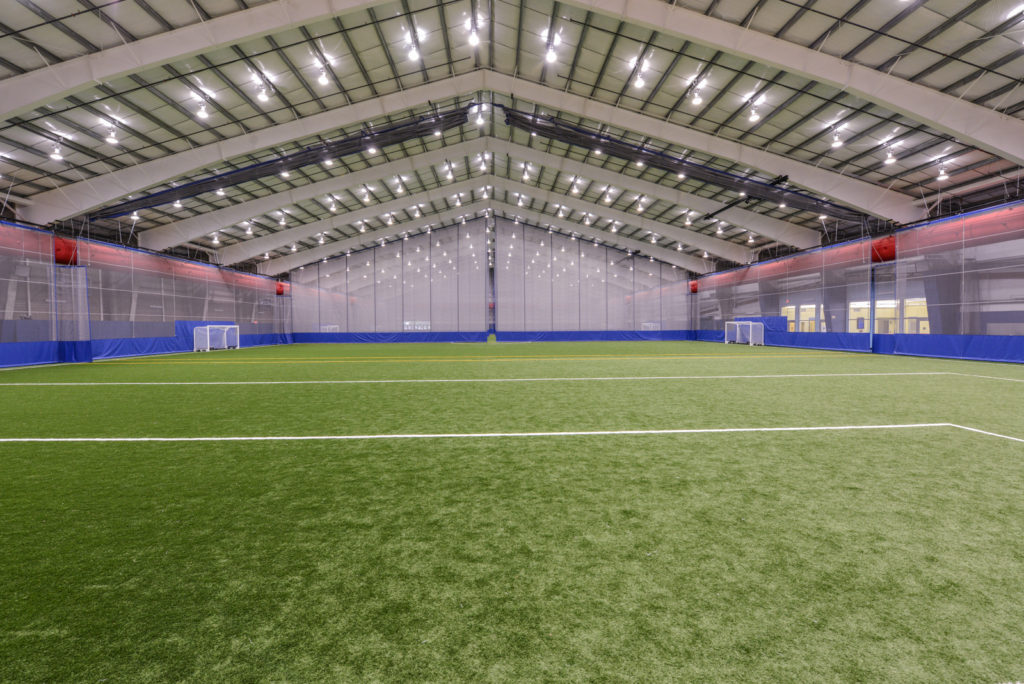
Our Project Managers
coordinated a collaborative design effort. When the design
neared completion. Putterman Project Managers revisited
the site with skilled field technicians to verify the accuracy of every measurement. Based on these precise field measurements, final changes were made to
the shop drawings before they were sent to fabrication.
Fabrication
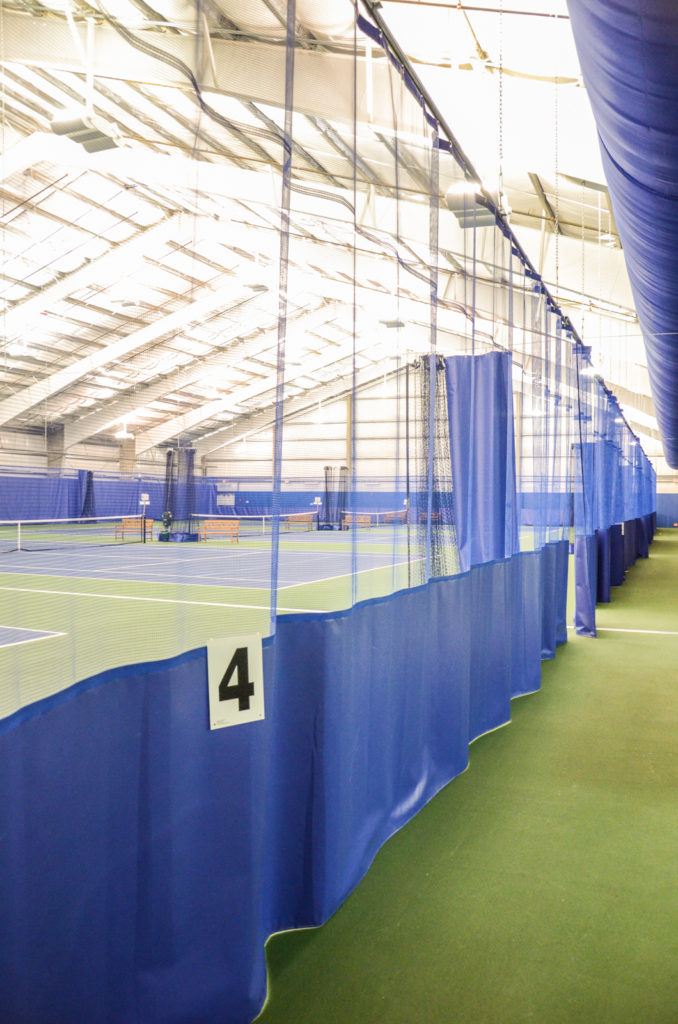
Fabrication for Chelsea Piers was kept on a very tight schedule. Following the procedure used during the quoting process of this
project, our Fabrication Team tackled production in phases. We shipped products to the Chelsea Piers site as they were completed, rather than waiting
to ship all the materials at once. This compartmentalized approach enabled Putterman installers to get underway ahead of schedule.
Installation and
Hardware
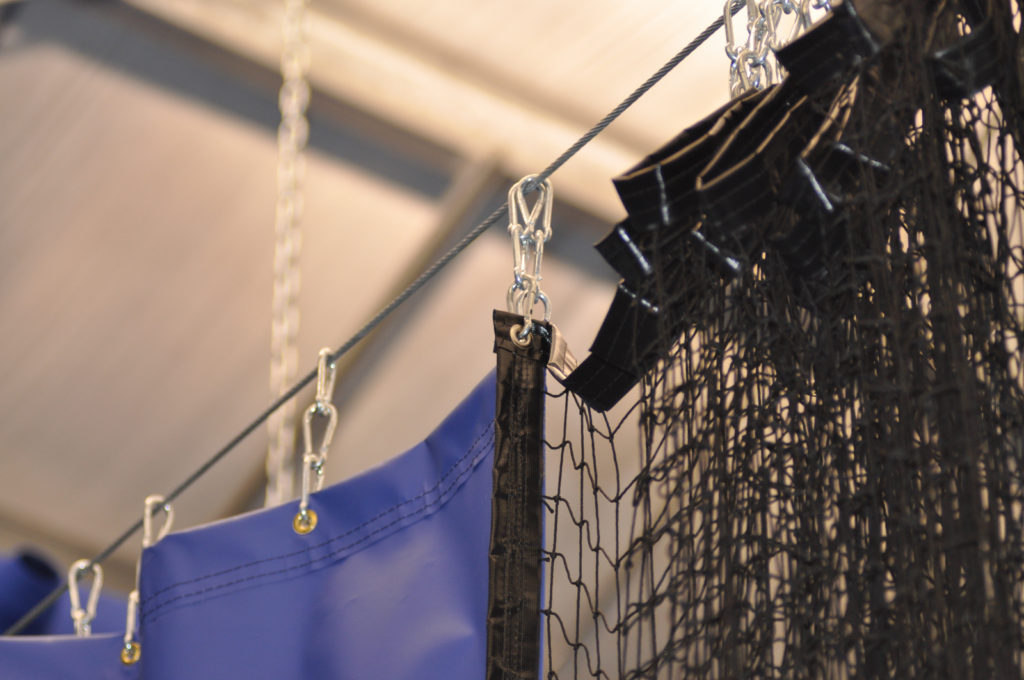
Putterman maintains a nationwide network of installers who work around the clock to satisfy our customers. By the time the fabricated materials arrived on-site, our Team was able to rapidly deploy the custom products while triple-checking that each aspect of the finished product was as expected by the customer. At Putterman Athletics we pride ourselves on coordinating every aspect of
large-scale installations, including equipment rental and hardware. Our Teams are available to work nights and weekends so that new product installation does not compete with our customers’ hours of
operation.
https://www.facebook.com/PuttermanAthletics